ICCP-SAM
ICCP-SAM
The ICCP-SAM tool represents a groundbreaking advancement in the field of offshore wind turbine maintenance and protection. Specifically developed to meet the demands of the new generation of turbines, which are larger in size, located in deeper waters, and often situated in regions with low salinity, the ICCP-SAM tool is set to revolutionize the industry.
Environment
- Reduction of secondary steel
- No pollution of aluminum waste
- Liftime externion possible
- No coating needed
Installation
- No installation vessel needed
- Transfer from people and tool
- OSV or CTV options
Design
- Design Freedom
- No secondary steel needed like Boatlanding or Skirt extension
Costs
- Cost reduction in installation
- Cost reduction in steel
- Less yard space needed
- One contractor / single point of contact
- Reduction of interfaces
Durable
- Outlive foundation.
- DNV approved.
- Durability test of connections
- Cable protection from the inside
Safety
- No diver intervention
- No cables on the outside
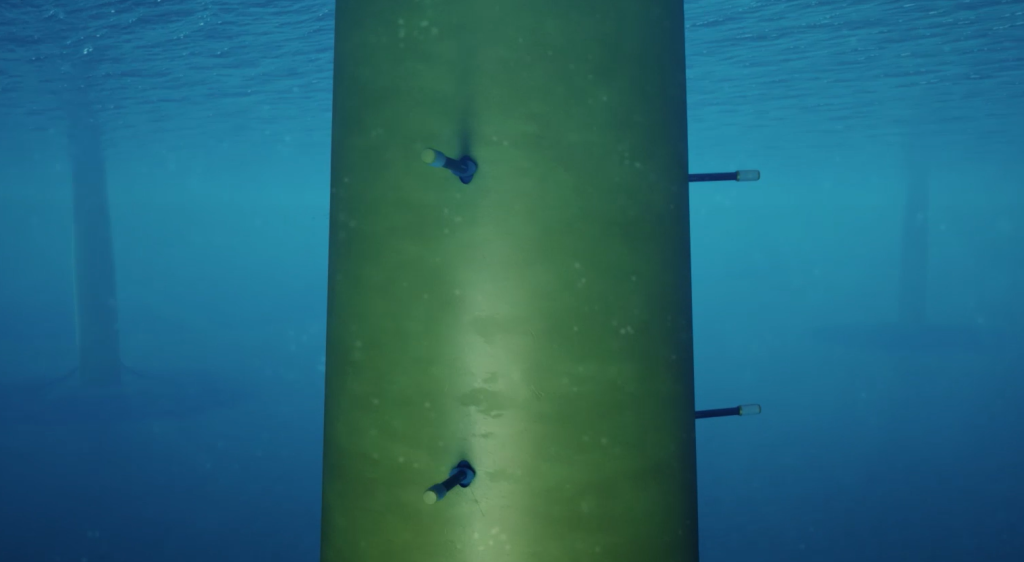
ICCP and SAM
The ICCP-SAM, an advanced technological solution meticulously engineered for the next generation of offshore wind turbines characterized by larger dimensions, deeper marine deployments, and operations in low-salinity areas, represents a significant collaboration between Bluestream, an OEG renewable company and CORROSION who have pooled extensive expertise and comprehensive field data to develop this DNV-approved, specialist-recognized tool that offers superior protection and maintenance capabilities, with the first installations of innovative ICCP anodes using the ICCP-SAM tool set to enhance the performance and reduce maintenance requirements of wind farms starting in 2025, thus setting a new benchmark in the offshore wind industry by ensuring robust protection and optimal efficiency for modern turbines.
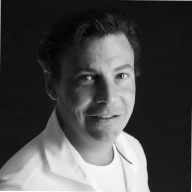
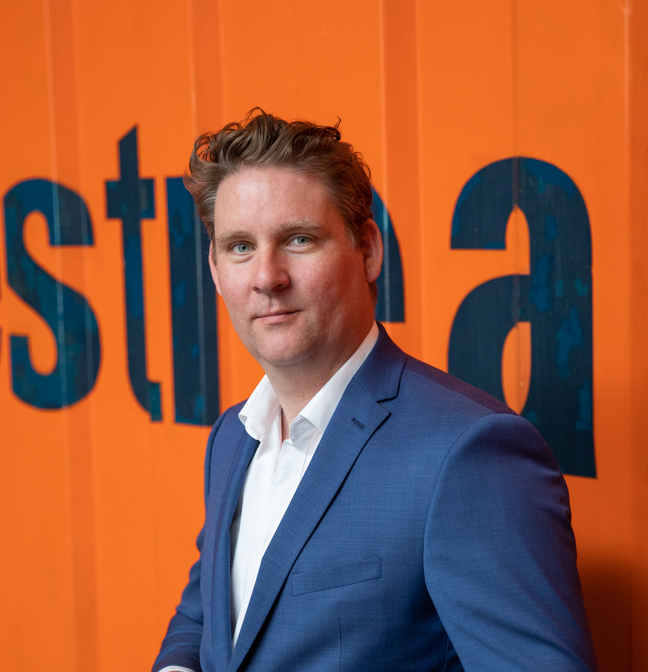
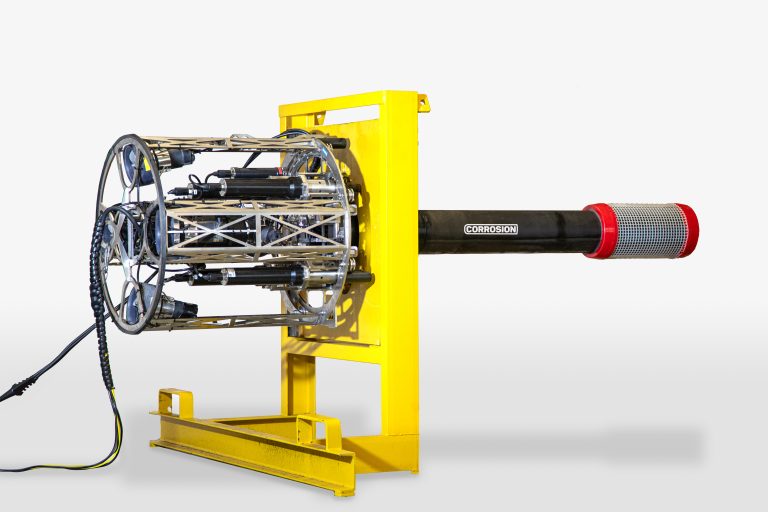
ICCP-SAM Specifications
ICCP-SAM specifications
MECHANICAL SPECIFICATIONS
- Space required to manipulate/rotate total assembly of 3000 mm
- Lifting arrangement above manholes/inside TP to mobilize and launch equipment (min 500kg)
- Flat-floor to drive material inside TP without having to lift. David arm where required to lift over
edges/thresholds - Possibility to place 10ft container on TP access deck, deck-load requirement 10T
- Cable hang-off point of ICCP anode inside ATP located close to wall and directly above aperture
for minimum cable suspension - ICCP hole dimensions: 300×500 elliptical
- ICCP hole location in vertical section of foundation
- ICCP holes not in-line/same orientation with the Cable Entry Holes, to prevent entanglement of
ICCP cable and power cable. This also helps installation purposes if power cables are already
installed - ICCP holes in-line with current direction to make installation easier and prevent sideway forces
on anode after installation. This condition is only valid IF the above conditions can be met as
well.
MANHOLE SPECIFICATIONS
- Manhole: 850×850 minimum (internal diameters)
- Each ICCP anode location requires a manhole directly above to make installation and control
easier and avoid cable clashes with power cables - The centre of the manhole needs to be >=2000 mm away from the monopile wall to provide
enough clearance between the ICCP anode tip and the monopile wall during installation. - Lifting arrangement above manhole/inside TP to mobilize and launch equipment ( min 500kg)
PAINT SPECIFICATIONS
- Contrasting area around ICCP hole inside MP for clear edge identification
- Contrasting line down from topside of foundation to ICCP hole for location purposes of correct
hole. Topside marking of ICCP heading/numbering